Carbide machining
What is carbide machining?
The Carbide machining comprises the machining or shaping of extremely hard materials consisting of a mixture of tungsten carbide particles and a binder such as cobalt. These materials are characterized by very high hardness and wear resistance, which is why they are often used in highly stressed components, cutting tools and wear parts. Due to this hardness, however, carbide is also particularly difficult to machine and poses a challenge for conventional cutting tools.
Challenges in carbide machining
Machining carbide presents a number of special challenges:
- High hardness and wear resistance: Carbide is extremely hard and resistant to wear. This means that conventional cutting materials, such as carbide itself, ceramic or high-speed steel (HSS), wear out quickly or are unable to machine the material effectively.
- Heat development: The high hardness of the material leads to high cutting forces and therefore also to considerable heat generation. This can damage both the tool and the workpiece.
- Brittleness: Carbide is hard, but also brittle. As a result, there is a risk of chipping or cracking during machining, especially if the tool is not optimally sharpened or the correct cutting speed is not used.
- High tool costs: Due to the rapid wear of conventional cutting materials when machining carbide, tool costs increase rapidly as new tools are required more frequently.
- Long processing times: Conventional machining processes, such as grinding with silicon carbide or electro-erosive machining, are often very time-consuming and lead to long production times.
How do you conventionally machine carbide without the use of diamond cutting materials?
Before the use of diamond cutting materials the machining of carbide was mainly carried out using the following conventional processes:
- Grinding with silicon carbide or aluminum oxide: These materials were used to machine carbide by abrasive grinding. However, the abrasives wear out quickly and the machining times are long.
- EDM (electrical discharge machining): In this process, carbide is machined by spark discharge. This process is very precise, but slow and expensive, particularly due to electrode wear.
- Cutting and milling with carbide tools: Carbide tools were also used, but they wore out quickly when cutting carbide, which led to frequent tool changes.
Advantages of diamond cutting materials
Diamond cutting materials have revolutionized the machining of carbide, as they can better overcome many of the aforementioned challenges:
- High hardness and wear resistance: Diamond is the hardest known material and far surpasses the hardness of carbide. As a result, diamond tools wear much more slowly than conventional cutting materials, which leads to significantly longer tool life. This means that fewer tool changes are required, which reduces production costs.
- More efficient heat dissipation: Diamond has very good thermal conductivity, which means that less heat is transferred to the tool and the workpiece during cutting. This minimizes thermal damage to the workpiece and extends tool life.
- Lower risk of outbreaks: The extreme sharpness of the diamond tools and the precise cutting action significantly reduce the risk of cracks or chipping on brittle carbide. This leads to higher machining quality and a lower scrap rate.
- Higher cutting speed and efficiency: Significantly higher cutting speeds can be achieved with diamond cutting materials, which drastically reduces machining times. This increases production efficiency and reduces operating costs.
- Better surface quality: Due to the high sharpness and precision of diamond tools, a better surface quality can be achieved, which often makes post-processing steps superfluous. This leads to faster production and higher product quality.
We offer the following diamond cutting materials:
The areas of application of PCD diamond are:
- Aluminium <10%Si
- Copper/tungsten copper
- Brass
- Composite materials such as CFRP/ GFRP
- Graphite
- PEEK
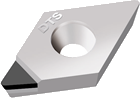
CVD-Thickfilm Diamond is ideally suited for processing highly abrasive materials such as:
- Aluminium >10%
- Plexiglass
- Copper/ Tungsten copper
- Glass- and Glass ceramic
- Carbide G-type >12% Co
- Carbide K-type >15% Co
- Titanum (Finishing operations)
- Any abrasive non-ferrous materials
- Other hard, brittle non-ferrous materials
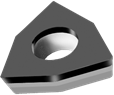
UltraDiamond is successfully used for processing:
- Carbide G-Sorte <12%
- Co Carbide K-type >7%Co
- Carbide with Ni Binder
- Glass- and Glass ceramic
- Quartz glass
- Other hard, brittle non-ferrous materials
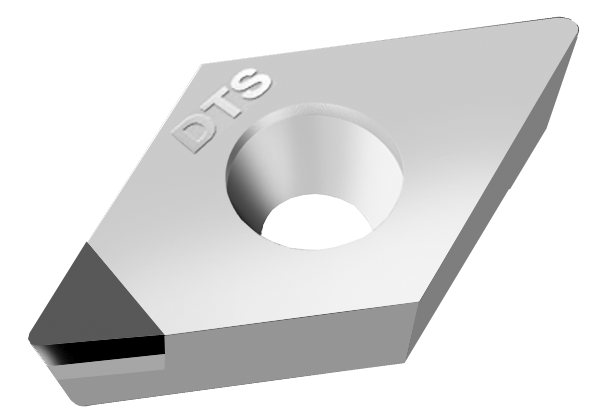
You want to know more about our diamond cutting materials?
Here you go! Just click here and you will be redirected to more information about them.
Here you will find high-quality diamond tools:
For high-quality diamond tools for efficient carbide machining, Diamond Tooling Systems DTS GmbH is your competent partner. With a wide range of specially developed diamond tools, we offer solutions for all challenges in carbide machining. Visit our webshop via the button below or contact our team of experts for individual advice and customized tool solutions.
Contact us!
DTS GmbH
Hans-Geiger-Strasse 11a
D-67661 Kaiserslautern
Customer service
Mo. - Fr. 8:00 - 16.30 Uhr
Contact details
F: +49 (0) 6301 32011-90