What is hard milling?
Hard milling is a special machining technique that is used for machining hardened materials with a hardness of more than 45 HRC (Rockwell hardness). This method is often used in the tool and mold making industry, where hardened components need to be precisely machined. Compared to traditional processes such as grinding or eroding, hard milling offers greater efficiency and flexibility, as complex shapes can be produced in a single machining step and without time-consuming reworking.
What can be processed with hard milling machines and what are the areas of application?
Hard milling is used particularly in industries in which hardened materials that are exposed to high mechanical loads are processed. Typical areas of application are:
- Tool and mold making: Here, hard milling is used for the finishing of molds and tools made of hardened steel, such as injection molds or punching tools.
- Automotive industry: Hard milling is often used in the production of engine and transmission parts as well as other components that have to meet high wear and load requirements.
- Aerospace: Hard milling is particularly suitable for machining high-strength materials used in engines or structural components.
Advantages of hard milling compared to conventional methods
- Higher productivity: Hard milling enables the direct machining of hardened materials without post-processing steps such as grinding or eroding. This means that machining processes can be carried out in a single operation, which shortens production times.
- More complex geometries: In contrast to conventional grinding processes, hard milling can produce complex 3D shapes and contours, which is particularly advantageous in mold making.
- Better surface quality: Modern hard milling tools achieve a high surface quality, which often makes further surface treatment superfluous. This makes the manufacturing process more efficient.
- Cost savings: The reduction in machining steps and higher productivity reduce production costs. The tools are also more durable, which minimizes tool changes.
- High precision: Very tight tolerances can be achieved with hard milling, resulting in precise components that meet the requirements of high-performance applications.
Challenges in hard milling
However, hard milling also places high demands on the cutting tools, as the materials are extremely hard and abrasive. Conventional milling tools wear out quickly or cannot deliver the desired cutting speeds and surface qualities. This makes the use of specialized, wear-resistant cutting materials necessary.
The advantage of diamond and CBN tools for hard milling
- CBN (cubic boron nitride): CBN tools are the preferred choice for hard milling of hardened steels as they offer excellent hardness and wear resistance. CBN can withstand temperatures of up to 1200 °C and is therefore ideal for machining hard materials at high cutting speeds.
- PCD (polycrystalline diamond): Diamond tools are not suitable for machining steel, but are suitable for materials such as fiber-reinforced plastics, ceramics and graphite, which are also used in hard milling.
- CVD-D (chemically vapor-deposited diamond): CVD-D tools are coated with a fine diamond layer, which is characterized by the CVD process (chemical vapor deposition). These tools are characterized by exceptional wear resistance and hardness, making them ideal for machining highly abrasive materials such as carbon fibre composites, graphite or ceramics. In contrast to PCD, CVD-D tools enable even greater precision in surface processing and have excellent thermal stability. These tools are used in particular for extremely abrasive machining where other cutting materials would wear out quickly.
Advantages of these tools:
- Longer service life: CBN and PCD tools have a significantly longer service life than conventional tools and enable continuous machining without frequent tool changes.
- High cutting speed: These materials enable high cutting speeds, which significantly reduces machining time.
- Higher precision and surface quality: Thanks to their extreme hardness and sharpness, CBN and PCD tools ensure precise cuts and a better surface quality without reworking.
For first-class tools for hard milling, including CBN and PCD milling tools, Diamond Tooling Systems DTS GmbH is your reliable partner. We offer a wide range of high-precision, durable cutting tools that have been specially developed for demanding hard milling applications. Visit our webshop or contact our team for individual advice and customized solutions for your requirements.
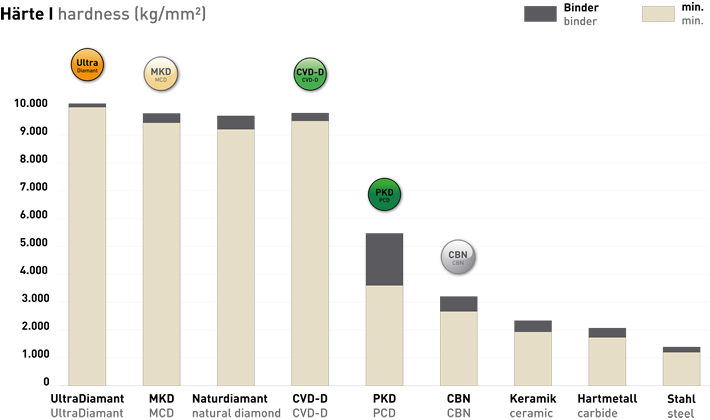
Contact us!
DTS GmbH
Hans-Geiger-Strasse 11a
D-67661 Kaiserslautern
Customer service
Mo. - Fr. 8:00 - 16.30 Uhr
Contact details
F: +49 (0) 6301 32011-90